 |
Our Services
|
|
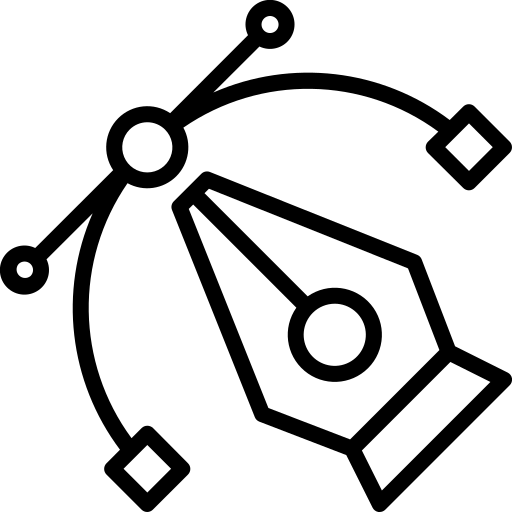 |
 |
Mold Design
|
 |
Our experienced engineering teams offer professional mold design services that adhere to DFMEA (Design Failure Modes and Effects Analysis) to achieve the highest quality, minimize costs and ensure reliable long-term production mold. The design process starts with detailed 3D engineering drawings using CAD software (SolidWorks or Pro E), 3D mold flow analysis to establish the best mold flow design. At PMM, we strive to deliver robust mold designs including cavity pressure sensors and cavity conformal cooling designs for the optimum cycle times. |
|
|
|
|
|
|
|
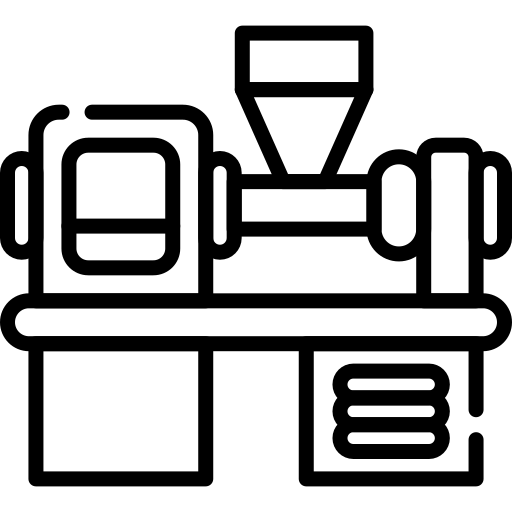 |
 |
Precision Mold Fabrication
|
 |
Equipped with high-tech automated CNC EDM, WEDM and high-speed CNC milling (RPM40,000), advanced measuring equipment and heat treatment furnace from top manufacturers in Japan and Germany, we are capable of delivering consistent high-quality molds with micro tolerances and surface finishing roughness ranging from VDI 18 (Ra0.80) to VDI 9 (Ra0.30). Further polishing can produce an ultrasmooth finish of VDI 3 (Ra0.15) for special applications. Via our process planning reviews, we are able to adopt the best machining process to decrease lead time and production costs with zero compromises in quality. |
|
|
|
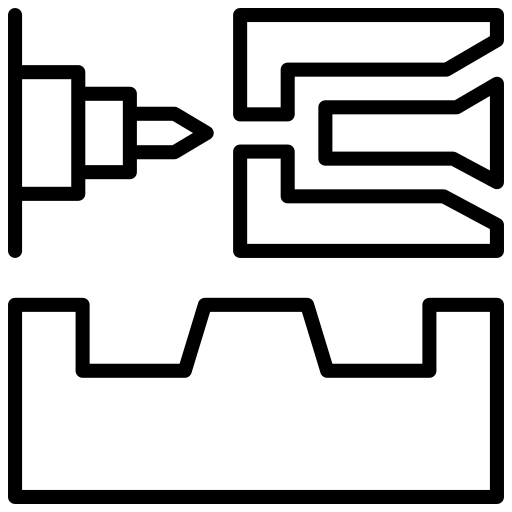 |
 |
Precision Injection Molding
|
 |
The molding facilities are set up with established Japan-branded precision plastic injection molding press ranging from 30 tons to 110 tons. We provide a stable production line led by a group of veteran molding process engineers and toolmakers. With the experienced molding team, we are able to improve and develop advanced process parameters by incorporating the latest molding technology which includes the cavity pressure sensor and hot runner system. Moving forward, we are targeting to streamlining production with highly automated systems. |
|
|
|
|
|
|
|
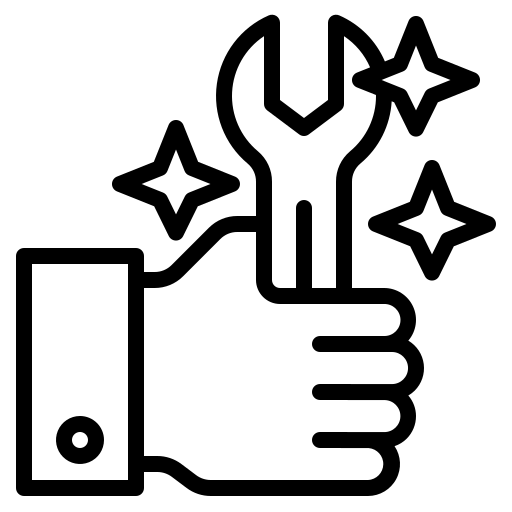 |
 |
One-Stop Services
|
 |
At PMM, we strive to deliver complete one-stop services that oversee precision plastic mold fabrication at every stage. From consultation, mold design, fabrication, finishing, and maintenance, the consolidation of services gives our team full control over production, working closely with customers to meet their exact product specifications and requirements. Our one-stop, in-house service solution also helps reduce costs, speed turn-around time, and facilitate easy follow-up services such as mold assembly, functional debugging & testing, first article inspection and mold conditioning to deliver better quality and outcomes. |
|
|
|